Prefer to listen? Press play to hear this article.
These devices have become essential tools in modern flight training, providing pilots with a highly realistic environment to practice and maintain their skills. But with constant training in rotation, these goliaths of flight training devices must be able to withstand it.
To ensure these complex systems remain operational and compliant with strict aviation regulations, rigorous maintenance routines for full flight simulators are in place. From daily system checks to long-term updates, maintaining an FFS is as demanding as servicing an actual aircraft. Let’s take a closer look at what goes into keeping these advanced training devices in top shape.
Daily, Weekly, and Monthly Maintenance Routines
Just like an aircraft undergoes rigorous pre-flight checks, a full flight simulator follows a strict maintenance schedule to keep it running smoothly. It wouldn’t be a surprise to say that such devices have to undergo daily inspections. With the amount of work these high-fidelity machines do, engineers have to attend to them very frequently and ensure every component, from lighting systems to software calibrations, is operational, ensuring the simulator mimics an actual aircraft flawlessly.
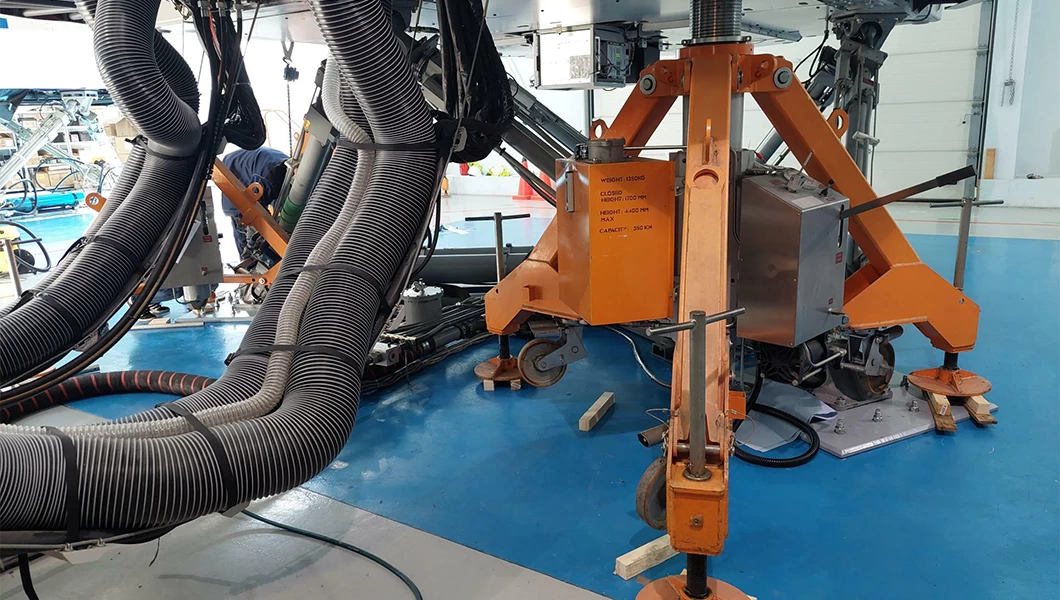
Routine tasks include structural adjustments, lubrication, and fine-tuning the controls, motion, and visual systems. This schedule is not only tailored to manufacturer guidelines but also to operational needs.
Weekly tasks include deeper system checks and minor calibrations, while monthly maintenance involves full system evaluations and software updates to prevent performance drift.
Think of it like a high-performance car: skip an oil change here and there, and soon enough, you’re facing an expensive repair bill. For a full flight simulator, that could mean costly downtime and disrupted training schedules.
Mitigating Downtime Risks
Proactive maintenance is key to preventing unexpected failures. Regular inspections and real-time data analysis allow engineers to address emerging issues before they escalate. However, some breakdowns remain unavoidable, making swift response protocols essential to minimizing disruptions in flight training schedules.
Data logging and monitoring’s importance also cannot be downplayed in simulator maintenance. Continuous tracking of performance data allows engineers to detect any irregularities early. Internal tools and software programs assist in calibration, part procurement, and audit preparation, ensuring seamless operations and optimized maintenance scheduling.
Calibration of Motion and Visual Systems
To keep it real in the cockpit, simulator manufacturers provide detailed calibration guidelines to maintain realism. Engineers meticulously adjust the motion system to reflect real aircraft behavior, ensuring that pilots experience authentic flight dynamics. The visual system undergoes fine-tuning to provide accurate environmental representation and minimal latency.
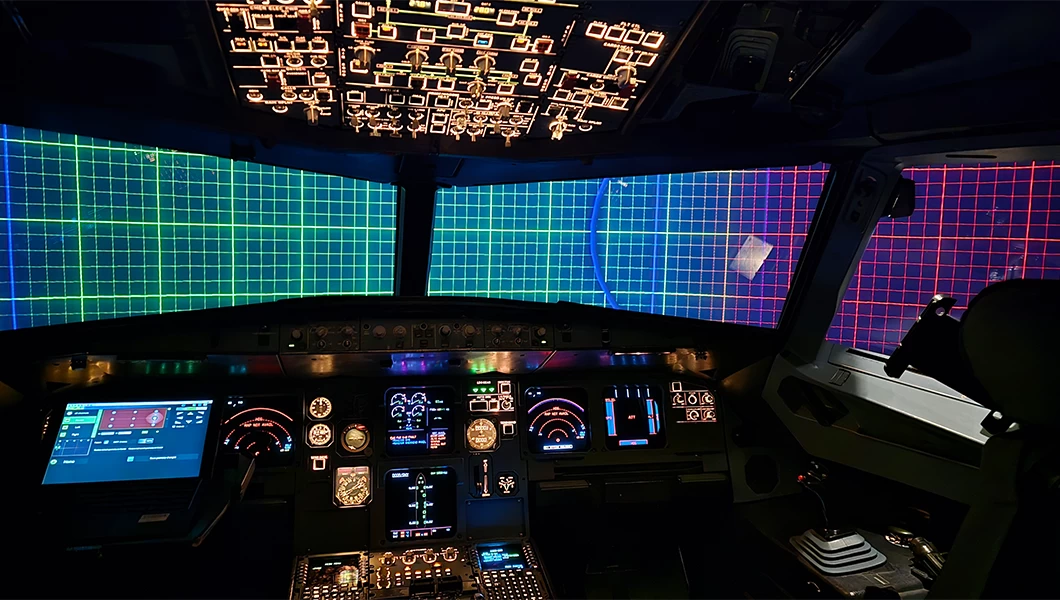
As per EASA regulations, databases related to navigation, aircraft data, terrain, and virtual landscapes must be regularly updated. This ensures that flight training remains accurate and prevents negative training effects.
Components Requiring Regular Maintenance
A full flight simulator is more than just a fancy cockpit mock-up—it’s a carefully engineered machine designed to replicate real-world flying conditions. The key players in this high-stakes performance include:
- Motion Systems – These hydraulic or electric actuators simulate the movement of an aircraft, allowing pilots to feel turbulence, banking, and even acceleration.
- Visual Systems – High-resolution projectors and domed screens create an immersive environment that replicates real-world flying conditions, including weather changes and night operations.
- Flight Deck Instruments – Every knob, switch, and display in the simulator must function just as it would in the actual aircraft to ensure muscle memory training is spot on.
A malfunction in any of these components can throw off the entire experience, leading to inaccurate training and failed regulatory compliance.
Essential Tools for Maintenance
To have this all under check, a wide range of specialized tools is required to maintain full flight simulators, from torque wrenches and force meters to video analysis systems. Advanced diagnostic equipment, such as latency tests and visual system projectors, ensures precise calibration and high-fidelity training experiences.
Ensuring Compliance with EASA Regulations
Staying within EASA regulations isn’t just about ticking boxes—it’s about ensuring the full flight simulator remains an accurate, safe, and effective training tool. This involves two types of evaluations done at different frequencies throughout the year.
Your PILOT CAREER
starts with a first click
Objective Evaluations
These assessments include running Qualification Test Guide (QTG) tests—averaging a whopping 161 tests per simulator type annually—to verify that aircraft systems, flight dynamics, and motion cues meet certification standards.
Preparation for official qualification tests involves engineers who have completed CS FTD training. These experts perform in-depth calibrations and test runs to ensure compliance with EASA’s baseline standards. Each simulator’s master QTG database, established during initial certification, serves as the benchmark for these assessments.
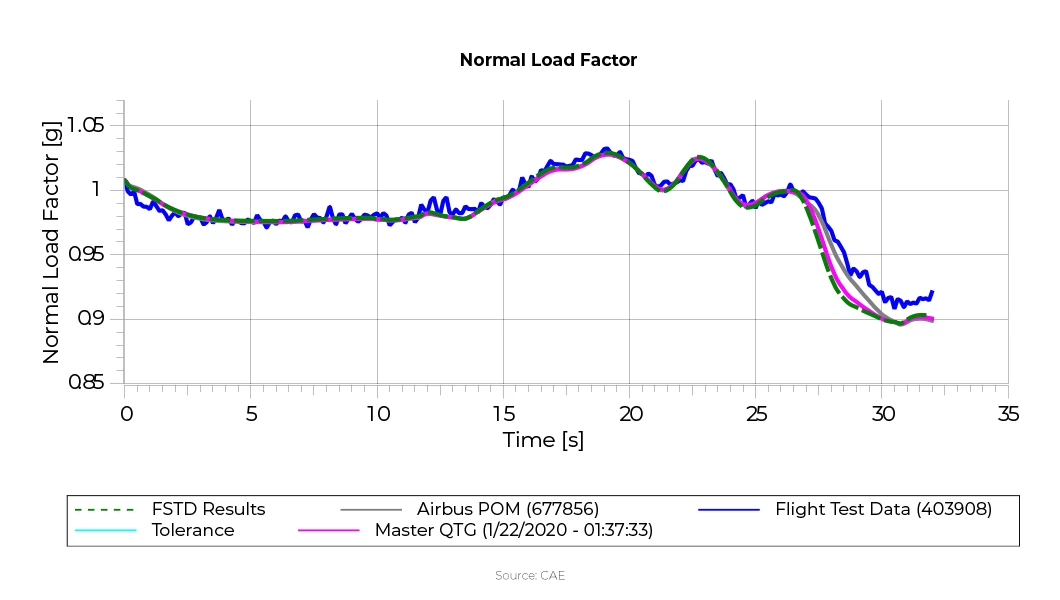

Subjective Assessments
Additionally, internal evaluations and flight tests by Subject Matter Experts (SMEs), like experienced pilots and engineers, help identify potential discrepancies before they become critical by conducting real-world scenario tests. The consequences of falling short on these assessments? Temporary or even permanent suspension of training programs.
Common Maintenance Challenges
One of the biggest challenges that full flight simulator engineers face is balancing maintenance schedules with client training needs. Precision planning is required to minimize downtime while ensuring the simulator remains fully functional. Another challenge is sourcing replacement parts, particularly for older simulators. While aircraft-related components can be found in the market, specific simulator parts often require partnerships with specialized suppliers or custom solutions.
The Future of Simulator Maintenance
The field of simulator maintenance continues to evolve. Advancements in computing power, software integration, and system automation are making maintenance processes more streamlined. Proactive approaches, including interactive diagnostics and real-time monitoring, ensure that FFS operations remain at the cutting edge of aviation training.
Looking ahead, simulator maintenance may steer more into integrating self-monitoring technologies. AI-driven predictive maintenance could enhance efficiency, reducing the need for constant manual oversight. However, human expertise will remain indispensable, as engineers and their knowledge are extremely important in fine-tuning and ensuring system reliability.
Bottom Line
In the end, maintaining a flight simulator is a mix of engineering prowess, technological foresight, and a dash of creativity. It’s not just about keeping the lights on—it’s about ensuring that the next generation of pilots gets the best training possible, every time they step into the cockpit.